Replacing O-rings and Header Gaskets on F250 Diesel Oil Cooler
How to tell if you need to change O-rings?
There are three big signs of a possible O-ring problem.
- Oil in coolant
- Coolant in oil
- Oil leaking from oil cooler
Because of the way the oil cooler is constructed, you won't see coolant leaking outside unless from one of the header gaskets.
The Problem
I couldn't find anything on the internet that explained what was involved in servicing the oil cooler. This really worried me since I had no idea what surprises might be involved. Turns out that this is really a pretty simple procedure if you know a few tricks. My truck is a 1996, but other years should be similar. I wrote this article to help anyone else who can't find information on this repair.
The Parts
You will need the following parts:
- Front header gasket
- Rear header gasket (Rear header includes oil filter mount)
- 2 smaller O-rings to seal water sections from oil section
- 2 larger O-rings to seal oil section from outside
The Tools
You will need the following tools:
- 10mm Socket with ratchet or breaker bar
- Short extension for rear header bolts (bolts are slightly recessed)
- about 2 feet worth of extensions (to reach front header bolts)
- Gasket scraper
- soft rubber mallet (don't use a regular hammer!)
- Bath towel or equivalent to pad parts during tapping
- screwdriver (to clean any scale on O-ring seats)
- Flashlight
- Helper (during reassembly, nice earlier but not necessary)
Removal
Tip: If you have a really messy, greasy mess underneath, put on some old clothes and goggles and get a hose with a strong jet spray nozzle. This will make a big mess and should be done the night before doing the work so that the water dries or it will drip on you for hours. The caked on oil and grease can be mostly blasted off with the water hose. Just make sure you don't spray the computer and its connectors which are on the firewall near the brake master cylinder. Watch out for the oily water bouncing back in your face (eyes). You will have to get underneath to get the job done and spray form every side and position. This will leave a lot of grease chunks all over so be sure to clean this up and pick a good place to make this mess. Also, watch out for loose parts that got trapped in the grease. You may find a lot of valuable bolts, nuts, parts and tools!
First, VERY IMPORTANT: Turn the truck on and turn the wheel all the way to the left. This will give you easy access to the two front header bolts later! Once you drain the oil and coolant, you can't start the truck!!
Second, remove the 110v cord from the block heater. It pulls straight out, the clip holding it on just pulls over the ridges that look like threads. You might need to open the clip a little, but mine wiggled free. Push it up out of the way.
Next, drain the oil and coolant and remove the oil filter
There are 3 10mm bolts in the rear header. One is a bit hard to find (all are very accessible), just study the header gaskets bolt holes and you will know where to search. Be sure to have a pan ready to catch the gusher of coolant that will come out once you loosen these bolts. This will probably get oil in it so don't plan on reusing this if you are trying to re-use coolant. You should probably just loosen these but not remove them completely until you remove the front header bolts.
Third, remove the front header bolts. You will need a long extension or two coming in from in front of the wheel. Go ahead and take them out all the way if you can. As long as the three parts stay locked together, the assembly won't fall down or out.
Next, return underneath and pull out the whole thing. It really can be done but you will need to gently twist and turn it until you get the angles right. You will need to be careful with the two fuel lines that it hits. If you are careful, you won't have a problem. A helper peeking in the front to guide you will help but isn't necessary. Watch out for oil or coolant pouring out. It could get in your eyes.
Disassembly of Cooler Parts
There are two tabs that look like they are for disassembling the cooler. Forget them, you will just break them off. Pay attention to how things are put together. One of the tabs fits in a notch. The other has no such notch to guide you. Don't worry, there is a great trick that will help. Just try to keep the cooler turned the same way and avoid swapping ends which would reverse flow. Not fatal, but better to keep things the same. Set the whole thing on the towel to protect the gasket sealing edges. Gently tap off one header with the rubber mallet. It should pop off fairly easily. Try to keep the openings that will be exposed that have the radiator fins up or you will get a lot of oil spilled out. Do the same for the other end.
Figure 1. - Side View of Oil Cooler.
A - Flange that smaller O-ring rides against. Water section is to the left of A.
B - Flange that larger O-ring rides against. Oil section starts at the right side of flange at A and ends at B.
C - Window to inside of tube where oil flows. Radiator-like heat fins not shown.
D - Tab that helps align everything with headers.
Note: I tried to show everything so things are not exactly where drawn and not to scale.
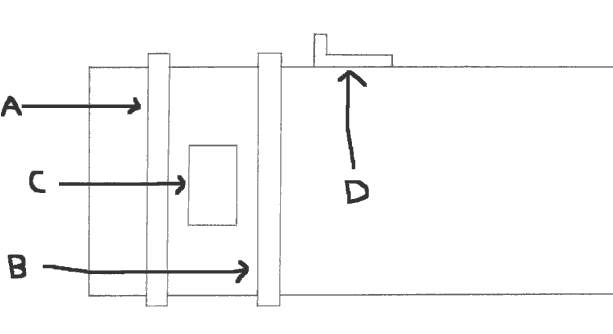
The header slides over the flanges and o-rings, stopping just before reaching the tab
The old small o-rings just slide off the ends of the pipe section, or are inside the header. The large o-rings have to slide over a metal lip. If they are old and hard, the best bet is to pry on them with a screwdriver until they break. (The new o-rings will easily slide on since they are flexible) You should try to get rid of as much oil as possible now since it will bother you later. You wont get it all. You can look down the water tubes to see if they are clogged or badly corroded. Mine looked a little bad in some spots but I couldn't decide if it was scale or corrosion. You may need to buy a new cooler. Some sites suggest a coolant system pressure test to diagnose the need for a new cooler. Obviously, you will need to replace the o-rings first or are almost guaranteed a false bad test. Clean everything up as much as possible. You will also need to use the gasket scraper on the headers and engine block to clean up the surfaces. I also found some corrosion or scale on the o-ring seat inside both headers. It looked just like metal from the factory so I almost left it there but if you have any bumps, be sure to scrape it off. It isn't supposed to be there. The o-ring needs to seat well or water will leak out into the oil or vice-versa
Figure 1. - End View of Oil Cooler.
A - Flange that smaller O-ring rides against.
B - Water tubes that run down length of oil cooler
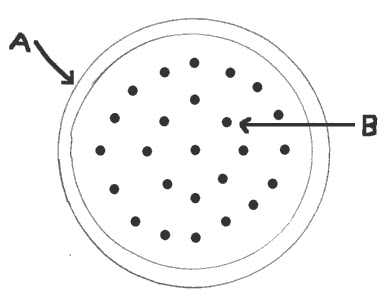
Be very sure to scrape the flared out ends of the headers where the pipe section goes. The flared out area starts the large O-ring and must be smooth and clean for an easy fit.
Reassembly of Cooler and Headers
Try to keep oil out of the water section of the headers. Water in the oil evaporates, but oil in the water stays and destroys the rubber parts in the cooling system. I used a very small amount of clean oil to lubricate the small o-rings, you can be generous with oil on the larger o-rings since they are only near the oil section of the cooler.
Please note that I make no guarantees about the correctness of the following procedure. There may be better methods and better tools to use. If you know a better way please let me know! For me, this method worked well and easily.
Put the towel flat on the floor. You will be attaching the oil filter header first. So put the pipe section standing up on the towel with the end that goes in the oil filter header up. Line up the notch with the tab I mentioned earlier. This will ensure the openings are lined up correctly. You must not start with the other header since it has no notch! If you can gently push the header on from above with a little wiggling, great. Otherwise, gently tap it on with the rubber mallet. Be sure not to tip the pipe or you could damaged the end on the floor with the tapping. When it is seated you will still be able to see the large o-ring a little but the metal lip is inside the header section. Now you pretty much have to have a helper.
Bunch up the towel and flip everything end over end to do the same with the other header. Be sure to protect the header on the bottom with the towel and to support it under the flattish section where the pipe section goes in. You will need a helper to steady things. How do you figure out where to turn the front header? You use a trick with your eyes that we use all the time in construction to exactly line things up. First, what you want is to have both gasket seats lined up since the engine block is a straight line. You can actually get it perfect. You don't need perfect though since the bolts will spin the header a little bit as long as you get it close enough to start the bolts in the block.
The trick: Your eye can line things up just right by looking down the gasket surface of the header lining it up with the other header's gasket seat. The problem is that your eye will deceive you a bit unless you are directly over the gasket seat. How do you do that? Put your eye over it more or less. As you move back and forth, the flat surface will appear and disappear. Move your head until you can see the flat part, now move back until it just barely disappears. You are now directly over things and can line the top section up perfectly with the bottom section. As you push or tap the two together, check the alignment again and turn things as needed. A tiny bit off won't matter, but with care you can line it up just right the first time.
Reattachment to Engine
You can now put the assembly back into the area it goes. With a helper's eye, you can even avoid getting the gasket areas dirty! Don't worry about the gaskets until you slip the whole thing back into the truck. Then, get out the gaskets and make sure you see how they go. Start the back section first since the block heater would get in the way later. Slip the gasket in where it goes and start the bolts a little. Leave things loose so you can move things up front. Now move to the front section. With one person working in front of the tire and the other underneath inserting the gasket, insert the 2 bolts on the end of the extension and screw in all the way but don't tighten until the 3 back bolts are also all the way in. The person underneath will need to lift the cooler up against the block to tighten the screws. Once all the screws are handtight, tighten everything up with the socket.
Put on a new oil filter and add oil. Be sure to fill up the filter with oil first or your engine won't have any oil for a long time. Replace the coolant, cleaning out any oil first if the cooling system was contaminated (I'll add details here later if I find a good procedure I like). Don't forget to plug back in the block heater cord. Check to make sure you didn't forget any o-rings. A forgotten smaller o-ring will possibly ruin the motor. A forgotten larger o-ring will make a big mess real quick.
Start it up. Don't rev it up until a few minutes after you get oil pressure on the gauge. I had a lot of air bubbles in the oil right after running it for a couple of minutes. Guess it was from the air caught in the cooler's fins inside the oil section. Check for leaks, inside too! Look at the dipstick and in the coolant bottle for the wrong stuff showing up. Enjoy!
Last Updated: June 22, 2007